The world of offset printing is a complex and fascinating one, offering high-quality prints for a variety of applications. However, professionals in the printing industry often encounter common print defects in offset jobs that can affect the final product’s quality. Understanding and addressing these issues is crucial for maintaining customer satisfaction and ensuring successful print runs. This article will explore the most frequent print defects in offset jobs, providing insights into their causes and offering practical solutions.
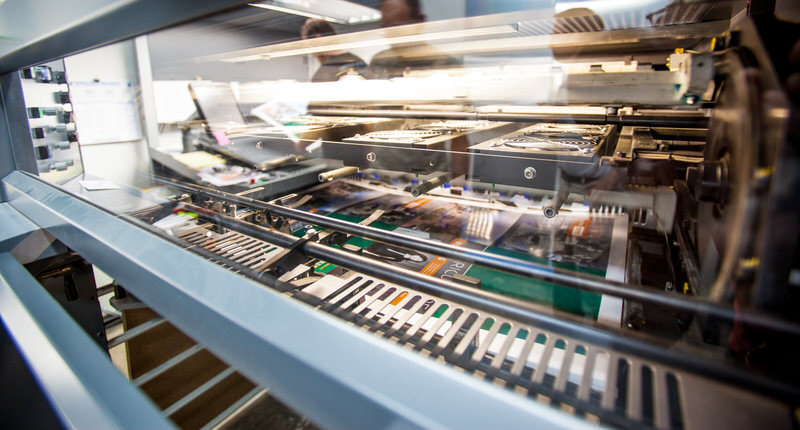
Understanding Offset Printing
Offset printing, also known as offset lithography, is a widely used printing technique that transfers ink from a plate to a rubber blanket and then onto the printing surface. This method is known for its ability to produce high-quality prints with rich colors and sharp details. However, like any printing process, it is not without its challenges. Learn more about offset printing here.
What Are Common Print Defects?
Print defects refer to any imperfections or errors that occur during the printing process, affecting the overall quality of the final product. In offset printing, these defects can range from color inconsistencies to registration errors. Understanding these defects and their underlying causes is the first step in effectively addressing them.
Color Inconsistencies
Color inconsistencies are one of the most common print defects in offset jobs. These can occur due to variations in ink density, improper ink mixing, or issues with the color calibration of the printing press. To address this, it is essential to regularly monitor and adjust ink levels, ensure proper ink mixing, and conduct regular color calibration checks.
Registration Errors
Registration errors occur when the different colors in a print job do not align correctly, resulting in a blurred or misaligned image. This can be caused by issues with the printing plates or the press’s mechanical components. To fix registration errors, it is crucial to regularly maintain and calibrate the printing press and ensure that the plates are correctly aligned. Troubleshoot registration errors effectively.
Ink Smudging
Ink smudging is another prevalent defect in offset printing, often caused by excessive ink application or improper drying. To prevent smudging, it is important to regulate the amount of ink used and ensure adequate drying time between print runs.
Ghosting
Ghosting refers to faint images or text appearing in unintended areas of a print job. This defect is often caused by ink and water imbalance or issues with the printing plates. To address ghosting, it is essential to maintain a proper ink-water balance and ensure that the plates are free from any residues or contaminants.
Preventive Measures for Common Print Defects
Prevention is always better than cure, and this holds true for offset printing as well. Implementing preventive measures can significantly reduce the occurrence of common print defects and improve print quality. Some effective preventive measures include:
Regular Equipment Maintenance
Regular maintenance of printing equipment is crucial for preventing print defects. This includes cleaning and calibrating the press, checking for wear and tear on components, and ensuring that all parts are functioning correctly.
Proper Ink and Paper Selection
Using high-quality ink and paper can significantly impact the final print quality. It is important to select the right type of ink and paper for each print job, considering factors such as color accuracy, drying time, and compatibility with the printing press.
Staff Training and Expertise
Having a well-trained and knowledgeable staff can make a significant difference in preventing print defects. Providing regular training sessions and keeping up with industry advancements can equip your team with the skills needed to identify and address potential issues before they become major problems. Explore more print techniques.
Conclusion
In the competitive world of offset printing, understanding and addressing common print defects is essential for maintaining high-quality standards and customer satisfaction. By identifying the root causes of these defects and implementing preventive measures, printing professionals can ensure successful print runs and deliver outstanding results to their clients.
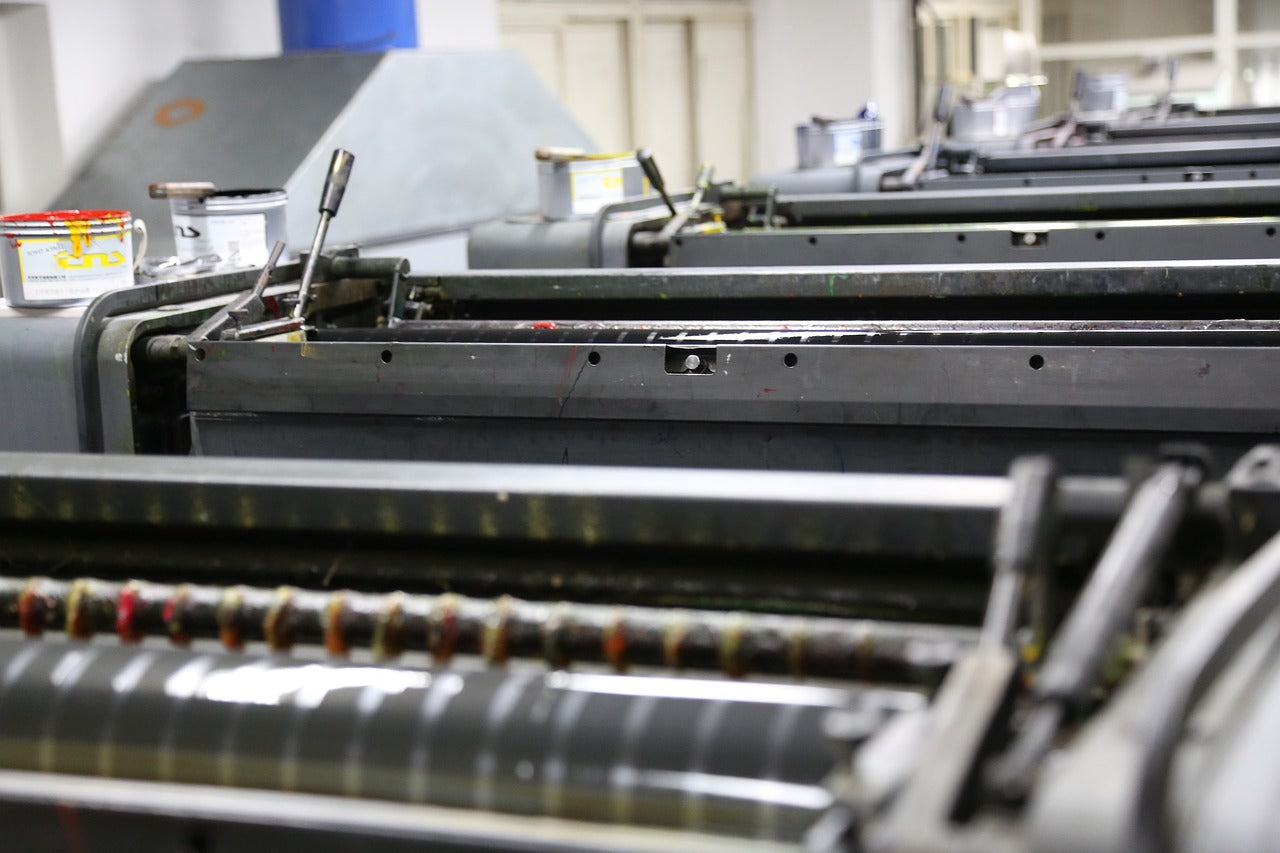
Frequently Asked Questions
What causes ink smudging in offset printing?
Ink smudging is often caused by excessive ink application or improper drying. To prevent smudging, it is important to regulate the amount of ink used and ensure adequate drying time between print runs.
How can I prevent registration errors?
To prevent registration errors, it is crucial to regularly maintain and calibrate the printing press and ensure that the plates are correctly aligned. Regular checks and maintenance can help avoid misalignment issues.
Why is color consistency important in offset printing?
Color consistency is crucial for producing high-quality prints with accurate and vibrant colors. Variations in color can affect the overall appearance of the final product, leading to customer dissatisfaction. Regular ink monitoring and color calibration can help maintain consistency.
This article contains affiliate links. We may earn a commission at no extra cost to you.