In the vibrant world of printing, offset printing stands as a cornerstone technology that has transformed the way we produce high-quality printed materials. Understanding how offset printing works is crucial for marketing professionals, designers, and anyone interested in the printing industry. This comprehensive guide will walk you through the intricacies of offset printing, detailing every step involved in the process and highlighting its advantages and applications.
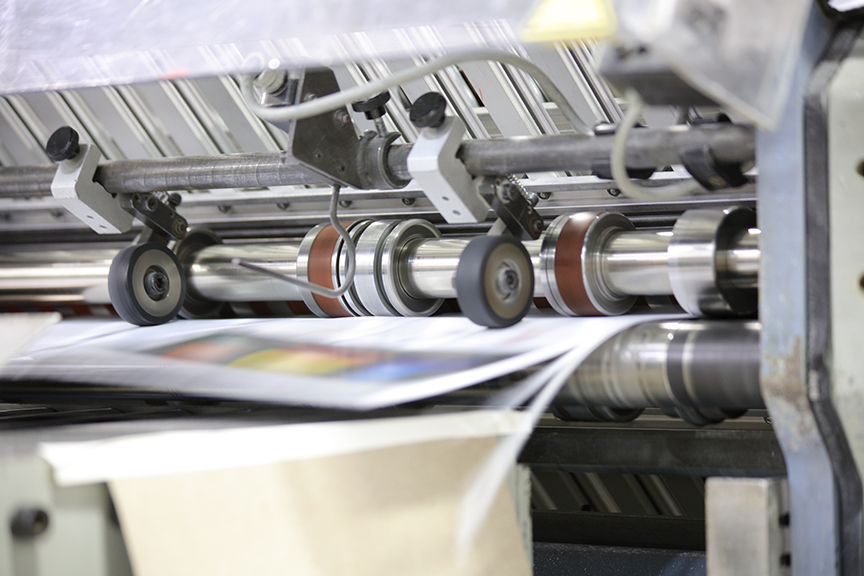
What is Offset Printing?
Offset printing is a widely used printing technique where the inked image is transferred from a plate to a rubber blanket, and then onto the printing surface. This method is called ‘offset’ because the ink is not directly applied to the paper. The process is known for its superior quality and cost-effectiveness, especially for large-scale print runs.
The History of Offset Printing
The origins of offset printing date back to the early 20th century. It was first developed by Ira Washington Rubel, who discovered that transferring an image to a rubber blanket before printing improved the quality of the print. Over the years, the technology has evolved significantly, becoming a dominant force in the printing industry.
The Role of Plates in Offset Printing
Plates play a pivotal role in the offset printing process. These plates are typically made from aluminum and have a rough surface that holds the ink. The image to be printed is etched onto the plate, and the non-image areas are treated to repel ink. This ensures that only the desired image is transferred onto the rubber blanket and then to the paper.
The Use of Rubber Blankets
Rubber blankets are essential in offset printing as they serve as the intermediary between the plate and the paper. They adapt to the texture of the paper, allowing for a smooth transfer of the image. This flexibility is what gives offset printing its high-quality results, even on rough or uneven surfaces.
The Offset Printing Process
Pre-Press Preparation
The first step in offset printing is the pre-press preparation. This involves creating the plates and adjusting the press settings to match the specifications of the print job. Color separation is also done at this stage to ensure accurate reproduction of images.
Inking the Plates
Once the plates are ready, they are inked using rollers that apply a precise amount of ink to the image areas. The non-image areas, treated to repel ink, remain clean and ensure that only the intended image is printed.
Transferring the Image
The inked image is transferred from the plate to the rubber blanket and then onto the paper. This two-step transfer process is what defines offset printing and contributes to its ability to produce sharp and clear prints.
Advantages of Offset Printing
High Quality and Consistency
One of the primary benefits of offset printing is its ability to produce high-quality prints with consistent results. The use of rubber blankets ensures that images are transferred smoothly, resulting in sharp and vibrant prints.
Cost-Effectiveness for Large Runs
For large print runs, offset printing is incredibly cost-effective. The setup costs are balanced by the low cost per unit, making it an ideal choice for bulk printing projects such as magazines, brochures, and packaging.
Versatility in Substrates
Offset printing is versatile in terms of the substrates it can print on. Whether it’s paper, cardboard, or even plastic, offset printing can handle a wide range of materials with ease, making it a preferred choice for diverse printing needs.
Applications of Offset Printing
Commercial Printing
Offset printing is extensively used in commercial printing for producing high-volume printed materials such as newspapers, brochures, and catalogs. Its ability to deliver high-quality prints consistently makes it a favorite among commercial printers.
Packaging
The packaging industry relies heavily on offset printing for printing boxes, labels, and other packaging materials. The versatility and quality of offset printing ensure that packaging designs are eye-catching and effective.
Publishing
In the publishing world, offset printing is the go-to method for printing books, magazines, and other publications. Its ability to produce large quantities quickly and efficiently makes it an indispensable tool for publishers.
Challenges in Offset Printing
Setup Costs
One of the challenges of offset printing is its initial setup cost, which can be high. However, for large print runs, these costs are offset by the low cost per unit, making it economically viable.
Environmental Concerns
The printing industry faces environmental challenges, and offset printing is no exception. The use of chemicals in plate making and the disposal of waste materials need to be managed responsibly to minimize environmental impact.
Future of Offset Printing
The future of offset printing looks promising as technology continues to evolve. Innovations in digital integration and eco-friendly practices are likely to enhance the efficiency and sustainability of offset printing, ensuring its relevance in the modern printing landscape.
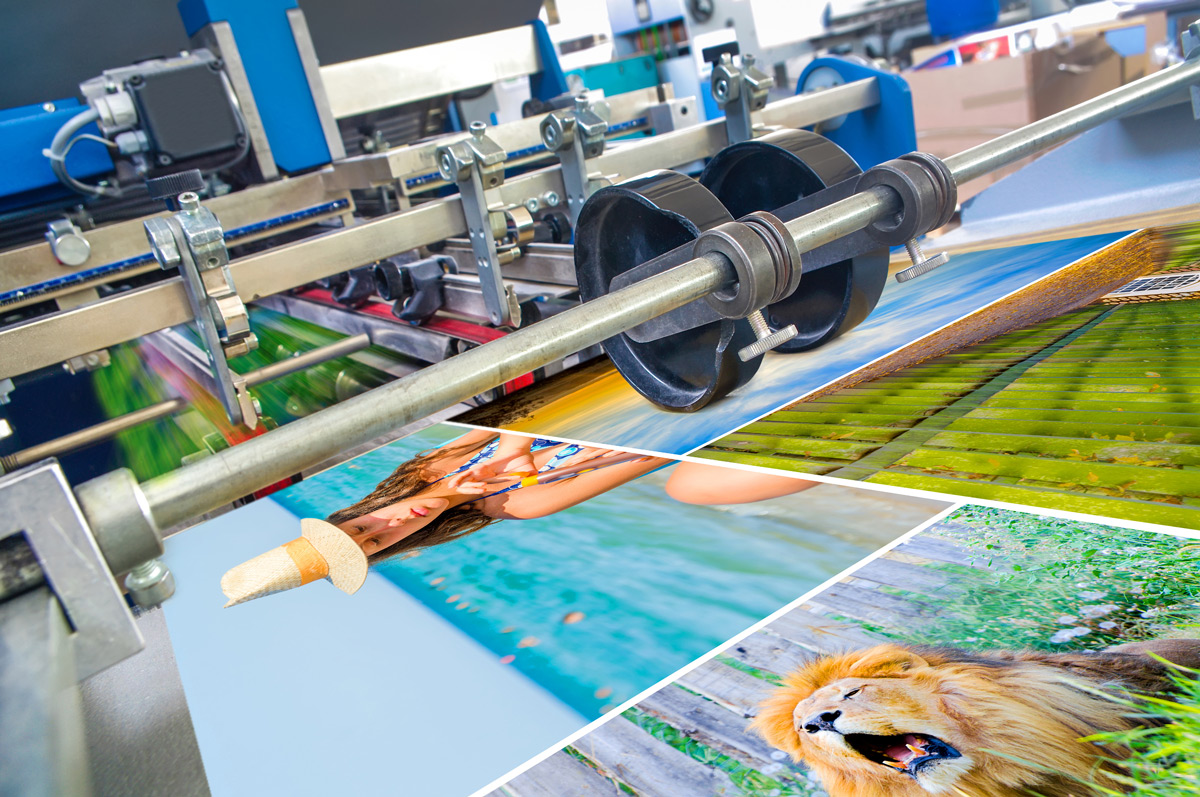
FAQs
What makes offset printing different from digital printing?
Offset printing uses plates and rubber blankets to transfer images, while digital printing prints directly onto the paper. Offset is ideal for large runs due to its cost-effectiveness and high quality.
Why is offset printing more cost-effective for large runs?
The initial setup costs of offset printing are high, but the cost per unit is low for large quantities, making it economical for bulk printing.
Can offset printing be environmentally friendly?
Yes, by adopting eco-friendly practices such as recycling and using sustainable materials, the environmental impact of offset printing can be minimized.
For more information about the intricacies of offset printing, you can visit this detailed guide.
For insights into the broader world of printing, explore topics like safety protocols and ink drying systems in flexo printing.
This article contains affiliate links. We may earn a commission at no extra cost to you.