When it comes to the world of offset printing, one of the most critical components that ensures the quality and efficiency of the printing process is the rubber blanket. In the initial stages of learning about offset lithography, professionals, especially marketers, may overlook this piece of equipment, yet its contribution is indispensable. Understanding the role of rubber blanket in offset is essential for anyone involved in the printing industry.
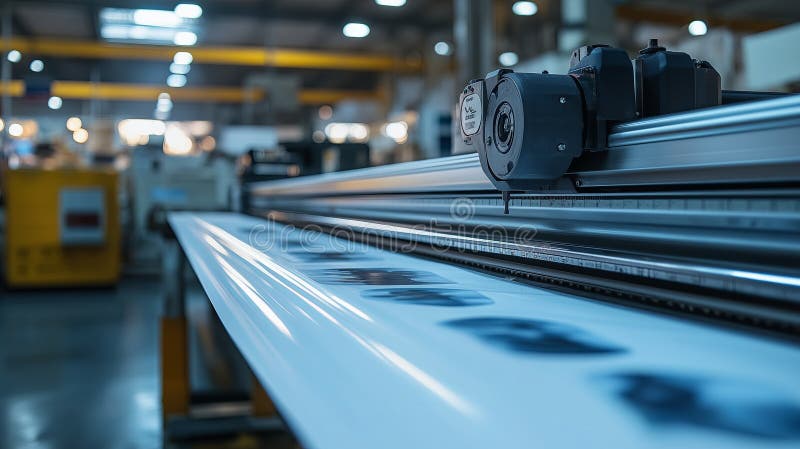
Understanding the Basics of Offset Printing
Offset printing is a widely used printing technique where the inked image is transferred from a plate to a rubber blanket, and then to the printing surface. This method is popular for high-volume print jobs like newspapers, magazines, and brochures. The process is beloved for its ability to produce consistent and high-quality prints.
For those unfamiliar with the intricacies of this process, a detailed guide on how offset printing works can provide further insights.
What is a Rubber Blanket?
The rubber blanket is a critical component in offset printing. It’s a synthetic rubber material that transfers the inked image from the plate to the paper. Its flexibility and durability make it ideal for handling the pressures of high-speed printing.
Composition and Design
Made from layers of rubber compounds, the rubber blanket is designed to withstand the rigors of the printing process. The top layer is smooth and ink-receptive, while the bottom layer provides cushioning to ensure even pressure distribution across the printing surface.
Importance in the Printing Process
The rubber blanket plays a vital role in ensuring that the image is transferred accurately and consistently. It provides a smooth surface that compensates for any irregularities in the paper, ensuring precise ink transfer.
How the Rubber Blanket Enhances Print Quality
The quality of the final print is heavily influenced by the condition and quality of the rubber blanket. A well-maintained blanket ensures that the ink is applied evenly, resulting in sharp and vibrant images.
Impact on Ink Distribution
The blanket aids in the even distribution of ink across the paper. This uniformity is crucial in preventing issues like smudging or streaking, which can compromise the quality of the printed material.
Durability and Maintenance
Regular maintenance of the rubber blanket is essential to maintain print quality. This includes regular cleaning and inspection for wear and tear. A compromised blanket can lead to increased downtime and higher costs due to reprints.
Challenges and Solutions
While the rubber blanket is vital for quality prints, it can pose challenges such as swelling from solvent exposure or wear from continuous use. Understanding these issues and implementing proper maintenance protocols can mitigate potential problems.
Common Problems
Common issues include blanket swelling, cracking, and glazing. Each of these can affect the print quality and should be addressed promptly.
Preventive Measures
Implementing a regular maintenance schedule and using high-quality materials can prolong the life of the rubber blanket. This includes choosing the right cleaning agents and handling the blanket with care during installation and removal.
Role of Rubber Blanket in Cost Efficiency
The rubber blanket also plays a part in the cost efficiency of offset printing. A durable and well-maintained blanket reduces the need for frequent replacements and minimizes production delays.
Reducing Waste
By ensuring consistent print quality, the rubber blanket helps reduce waste from misprints and reprints, contributing to more sustainable printing practices.
Optimizing Production Time
Minimizing downtime due to blanket issues means that print jobs can be completed faster, increasing the overall efficiency of the printing process.
Conclusion
The role of rubber blanket in offset printing is both fundamental and multifaceted. From ensuring high-quality prints to optimizing production efficiency, the rubber blanket is an essential component that cannot be overlooked. By understanding its importance and maintaining it properly, printing professionals can ensure consistent results and operational efficiency.
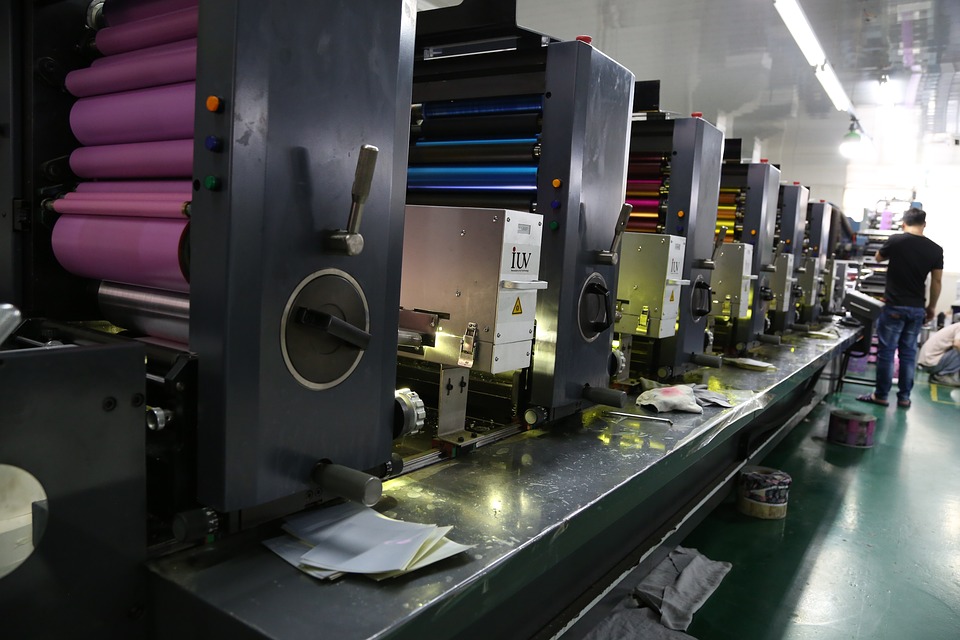
FAQs
What is the primary function of a rubber blanket in offset printing?
The primary function of the rubber blanket in offset printing is to transfer the inked image from the plate to the paper, ensuring high-quality and consistent prints.
How often should rubber blankets be replaced?
The replacement frequency of a rubber blanket depends on the volume of printing and the maintenance practices in place. Regular inspection can help determine when a replacement is needed.
What are common issues faced with rubber blankets?
Common issues include swelling, cracking, and glazing, all of which can affect print quality. Regular maintenance and proper handling can prevent these problems.
For more information on offset printing, you can read this in-depth guide.
This article contains affiliate links. We may earn a commission at no extra cost to you.